Less engine braking, lighter throttle
Re: Less engine braking, lighter throttle
So engine braking effects can be felt in two ways:
1. As you downshift, revs drop due to the shut throttle.
Letting the clutch back out engages the rear wheel to engine connection, and the effect of the engine increasing revs to bring it to the speed dictated by the primary and secondary gearing and rear wheel is felt as a decelerative force on the bike and rider.
This is the "jolt" you feel if you don't match revs to hear when downshifting- and causes rear wheel-hopping when downshifting too fast, or at too-high revs, so that when letting the clutch out the engine is being asked to rev higher than the rev limit.
Then, after the rear wheel and engine speed are once again fully synchronised:-
2. The force required to keep the engine turning at the revs dictated by primary and secondary gearing, against a closed throttle- or, rather, a throttle closed more than the point at which engine power being produced equals the force exerted by the rear wheel and drivetrain. Often described as a "neutral" throttle; neither accelerating or engine-braking.
The forces concerned are a combination of pumping losses below the piston(s) and also the effect of the engine acting as a gas pump.
The engine, if turning in the usual direction, pumps gasses (atmosphere plus any atomised fuel) in through the carbs and out through the the exhaust.
But by closing the throttle, you prevent enough gas flowing into the carbs, and the result is that the engine braking effect is increased- the engine is trying to suck air in against a "vacuum"- (not a real vacuum but a lower flow rate than the pumping piston is trying to achieve).
So what effect would a lighter flywheel (or crank, clutch, lighter rear wheel or a 520 chain and sprocket set) have?
In 1 above, the braking effect experienced would be decreased, as the rear wheel will be trying to increase the speed of the engine's rotational mass as before, but there is less mass to change, with a lightened flywheel.
Think of it as inertia- acceleration or deceleration of a given mass takes energy, but the more mass the more energy required to change its revs per minute; this applies equally to increasing revs as to decreasing revs.
In 2 above, a lighter flywheel or other rotating/drivetrain mass reduction would decrease the inertia of the rotating mass.
This results in an effect where the speed of change of the rotating masses takes less energy to acheive- this is felt as a decrease in engine braking.
However, this effect is small in comparison to the "sucking against a vacuum" effect described above.
The larger force is the one that takes precedence, and the decrease in mass is not noticed.
I mentioned pumping losses below the pistons- although the crankcases are open to atmosphere via the two cam cover to airbox breathers, the volume of air that can flow through this is small, and there is no way that enough air can flow through the breathers at the required flow rates, even at low revs.
As the crankcases are therefore effectively a closed volume, as each piston drops to BDC, the pressure underneath it increases, and then, as it rises to TDC the pressure beneath the piston drops.
Vee twins aren't easy to calculate properly, because the pistons don't rise and fall synchrously, they are staggered
Suffice to say that it takes some energy to increase a great venue volume's pressure (for proof, touch the metal parts of a tyre compressor or hand pump after use) even though the compressed air acts as a spring after BDC, pushing the piston up again.
But you can't get something for nothing, and every process has its losses (see laws of thermodynamics) and so the gas beneath the pistons, changing in volume and alteratively being compressed and decompressed, absorbs some energy.
(That's the principle behind the Krankvent, but as explored in another thread, makes no measurable difference to engine bhp or torque in real-life).
Phew!
If anyone with any proper knowledge can comment, please feel free, the above is just my basic understanding of physics, and I failed the o-level........
(O-level; I couldn't even spell GSCE)......
Is that input enough for you?
1. As you downshift, revs drop due to the shut throttle.
Letting the clutch back out engages the rear wheel to engine connection, and the effect of the engine increasing revs to bring it to the speed dictated by the primary and secondary gearing and rear wheel is felt as a decelerative force on the bike and rider.
This is the "jolt" you feel if you don't match revs to hear when downshifting- and causes rear wheel-hopping when downshifting too fast, or at too-high revs, so that when letting the clutch out the engine is being asked to rev higher than the rev limit.
Then, after the rear wheel and engine speed are once again fully synchronised:-
2. The force required to keep the engine turning at the revs dictated by primary and secondary gearing, against a closed throttle- or, rather, a throttle closed more than the point at which engine power being produced equals the force exerted by the rear wheel and drivetrain. Often described as a "neutral" throttle; neither accelerating or engine-braking.
The forces concerned are a combination of pumping losses below the piston(s) and also the effect of the engine acting as a gas pump.
The engine, if turning in the usual direction, pumps gasses (atmosphere plus any atomised fuel) in through the carbs and out through the the exhaust.
But by closing the throttle, you prevent enough gas flowing into the carbs, and the result is that the engine braking effect is increased- the engine is trying to suck air in against a "vacuum"- (not a real vacuum but a lower flow rate than the pumping piston is trying to achieve).
So what effect would a lighter flywheel (or crank, clutch, lighter rear wheel or a 520 chain and sprocket set) have?
In 1 above, the braking effect experienced would be decreased, as the rear wheel will be trying to increase the speed of the engine's rotational mass as before, but there is less mass to change, with a lightened flywheel.
Think of it as inertia- acceleration or deceleration of a given mass takes energy, but the more mass the more energy required to change its revs per minute; this applies equally to increasing revs as to decreasing revs.
In 2 above, a lighter flywheel or other rotating/drivetrain mass reduction would decrease the inertia of the rotating mass.
This results in an effect where the speed of change of the rotating masses takes less energy to acheive- this is felt as a decrease in engine braking.
However, this effect is small in comparison to the "sucking against a vacuum" effect described above.
The larger force is the one that takes precedence, and the decrease in mass is not noticed.
I mentioned pumping losses below the pistons- although the crankcases are open to atmosphere via the two cam cover to airbox breathers, the volume of air that can flow through this is small, and there is no way that enough air can flow through the breathers at the required flow rates, even at low revs.
As the crankcases are therefore effectively a closed volume, as each piston drops to BDC, the pressure underneath it increases, and then, as it rises to TDC the pressure beneath the piston drops.
Vee twins aren't easy to calculate properly, because the pistons don't rise and fall synchrously, they are staggered
Suffice to say that it takes some energy to increase a great venue volume's pressure (for proof, touch the metal parts of a tyre compressor or hand pump after use) even though the compressed air acts as a spring after BDC, pushing the piston up again.
But you can't get something for nothing, and every process has its losses (see laws of thermodynamics) and so the gas beneath the pistons, changing in volume and alteratively being compressed and decompressed, absorbs some energy.
(That's the principle behind the Krankvent, but as explored in another thread, makes no measurable difference to engine bhp or torque in real-life).
Phew!
If anyone with any proper knowledge can comment, please feel free, the above is just my basic understanding of physics, and I failed the o-level........
(O-level; I couldn't even spell GSCE)......
Is that input enough for you?
It's not falling off, it's an upgrade opportunity.
- KermitLeFrog
- Posts: 1662
- Joined: Sat Apr 11, 2015 6:44 pm
- Location: Hexham
Re: Less engine braking, lighter throttle
Thanks Tony. I didn't do Physics at A level but I do have a Mechanical Engineering degree (with honours) and I can't see much wrong with your analysis.
My dislike of engine braking is more aligned with your second scenario. Your first scenario can be mitigated with good throttle and clutch control. My Aprilia has very sophisticated electronics and has three engine maps which mainly effect engine braking. I've investigated the maps which can be downloaded and examined, or even changed if you are brave. The major difference between the "Sport" map (maximum engine braking" and the "Race" map (minimum engine braking and the one I prefer) is the "Gas" parameter. I'm sure it's more complicated than this but in Sport mode closed throttle gives 0% Gas. In Race mode closed throttle gives 5% gas. I know this is FI and completely different to the Storm's carbs but it indicates to me that keeping the butterflies open a bit more will reduce engine braking under a closed throttle.
But, as you say, addressing pumping losses may be the way to go. It should be easy to fit a large bore crankcase breather. I think Fabio has one fitted into the oil filler cap? I suppose you could also tap one into the top of the clutch cover. Just make sure you run the large bore hose up to a high catch tank. I wonder what sort of bore size you would need?
My dislike of engine braking is more aligned with your second scenario. Your first scenario can be mitigated with good throttle and clutch control. My Aprilia has very sophisticated electronics and has three engine maps which mainly effect engine braking. I've investigated the maps which can be downloaded and examined, or even changed if you are brave. The major difference between the "Sport" map (maximum engine braking" and the "Race" map (minimum engine braking and the one I prefer) is the "Gas" parameter. I'm sure it's more complicated than this but in Sport mode closed throttle gives 0% Gas. In Race mode closed throttle gives 5% gas. I know this is FI and completely different to the Storm's carbs but it indicates to me that keeping the butterflies open a bit more will reduce engine braking under a closed throttle.
But, as you say, addressing pumping losses may be the way to go. It should be easy to fit a large bore crankcase breather. I think Fabio has one fitted into the oil filler cap? I suppose you could also tap one into the top of the clutch cover. Just make sure you run the large bore hose up to a high catch tank. I wonder what sort of bore size you would need?
"I spent a lot of money on booze, birds and fast cars. The rest I squandered" (George Best, RIP)
Re: Less engine braking, lighter throttle
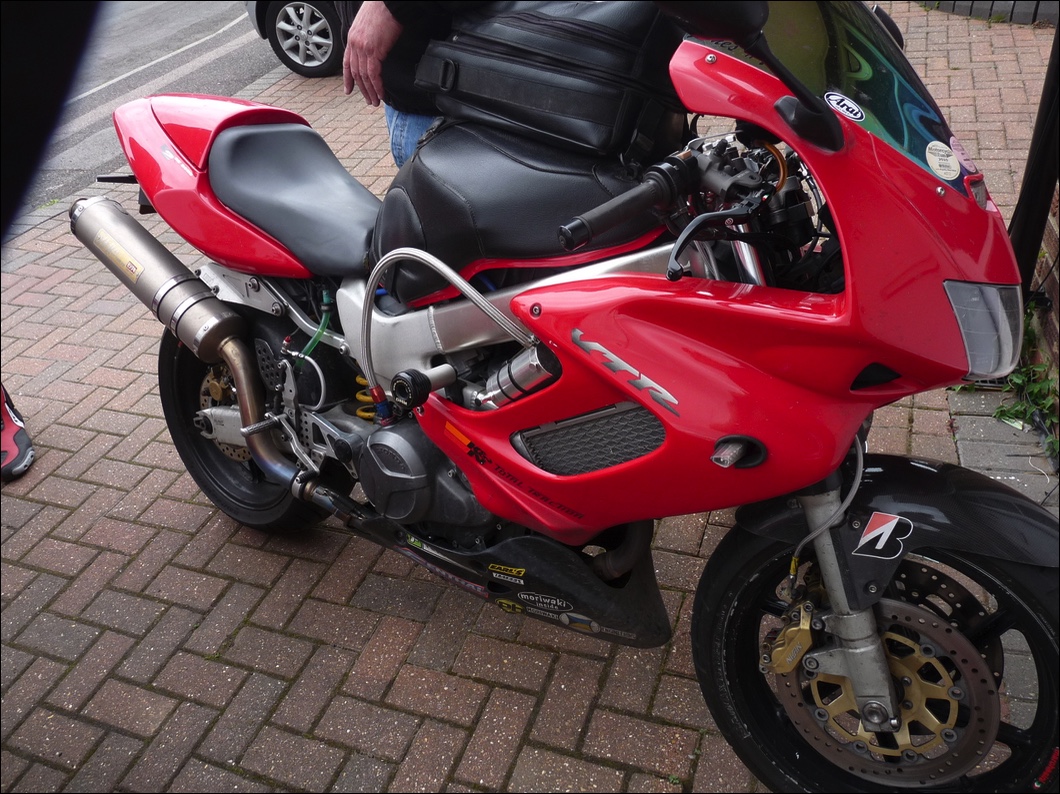
It may be that your whole purpose in life is simply to serve as a warning to others.
VTR Firestorm and other bikes t-shirts

Re: Less engine braking, lighter throttle
Ahh now see I own this bike now & the extra plumbing as seen here, wasn't on the bike when I bought it...
The oil filler cap is not std & I assume its something to do with this plumbing...
You'll have to ask Jonesey, a/ why he took it off..b/ what happened to it...
Making up since 2007, sometimes it's true...Honest...
Re: Less engine braking, lighter throttle
A lot of euro 4 bikes feel rough on pickup from a closed throttle because they have to have 0% fuel flow to meet emissions regs.
All of the remap and reflash solutions involve changing this to allowing some fuel in, which stops the jolt on pickup as you roll power on.
Lately, new versions of existing designs often have increased porting in the crankcase webs under the cylinders to allow air to flow more effectively under each piston to adacent sections of the cases.
As to a large-bore breather, most of the effect is due to adding the tube volume to the crankcase volume.
You might want to explore putting a thick machined gasket on the sump; thus acheives the same without getting messy oily air everywhere.
I ran a breather externally to the airbox to leave more airbox volume, but there was always a bit of oil film behind the filter.
All of the remap and reflash solutions involve changing this to allowing some fuel in, which stops the jolt on pickup as you roll power on.
Lately, new versions of existing designs often have increased porting in the crankcase webs under the cylinders to allow air to flow more effectively under each piston to adacent sections of the cases.
As to a large-bore breather, most of the effect is due to adding the tube volume to the crankcase volume.
You might want to explore putting a thick machined gasket on the sump; thus acheives the same without getting messy oily air everywhere.
I ran a breather externally to the airbox to leave more airbox volume, but there was always a bit of oil film behind the filter.
It's not falling off, it's an upgrade opportunity.
Re: Less engine braking, lighter throttle
MacV2 wrote: ↑Fri Dec 21, 2018 2:30 pmAhh now see I own this bike now & the extra plumbing as seen here, wasn't on the bike when I bought it...
The oil filler cap is not std & I assume its something to do with this plumbing...
You'll have to ask Jonesey, a/ why he took it off..b/ what happened to it...
Having checked with the ex master baker apparently the breather tank & plumbing was sold...to a sidecar racer or something...
Making up since 2007, sometimes it's true...Honest...
Re: Less engine braking, lighter throttle
thats something along the lines of what i have fitted, tho not as long in the pipework
. but i run mine into a catchtank behind the R/H rad... i did try it without it and just the normal filler cap when i got mine dynoed.. the difference was picked up by the machine. when i put my breather pipe back on i got a whopping extra 1.5 bhp lol.
so its helping but not so you can feel it, but as tescos say,every little helps

so its helping but not so you can feel it, but as tescos say,every little helps

the older i get,the faster i was 

Re: Less engine braking, lighter throttle
tony.mon wrote: ↑Fri Dec 21, 2018 12:25 am So engine braking effects can be felt in two ways:
1. As you downshift, revs drop due to the shut throttle.
Letting the clutch back out engages the rear wheel to engine connection, and the effect of the engine increasing revs to bring it to the speed dictated by the primary and secondary gearing and rear wheel is felt as a decelerative force on the bike and rider.
This is the "jolt" you feel if you don't match revs to hear when downshifting- and causes rear wheel-hopping when downshifting too fast, or at too-high revs, so that when letting the clutch out the engine is being asked to rev higher than the rev limit.
Then, after the rear wheel and engine speed are once again fully synchronised:-
2. The force required to keep the engine turning at the revs dictated by primary and secondary gearing, against a closed throttle- or, rather, a throttle closed more than the point at which engine power being produced equals the force exerted by the rear wheel and drivetrain. Often described as a "neutral" throttle; neither accelerating or engine-braking.
The forces concerned are a combination of pumping losses below the piston(s) and also the effect of the engine acting as a gas pump.
The engine, if turning in the usual direction, pumps gasses (atmosphere plus any atomised fuel) in through the carbs and out through the the exhaust.
But by closing the throttle, you prevent enough gas flowing into the carbs, and the result is that the engine braking effect is increased- the engine is trying to suck air in against a "vacuum"- (not a real vacuum but a lower flow rate than the pumping piston is trying to achieve).
So what effect would a lighter flywheel (or crank, clutch, lighter rear wheel or a 520 chain and sprocket set) have?
In 1 above, the braking effect experienced would be decreased, as the rear wheel will be trying to increase the speed of the engine's rotational mass as before, but there is less mass to change, with a lightened flywheel.
Think of it as inertia- acceleration or deceleration of a given mass takes energy, but the more mass the more energy required to change its revs per minute; this applies equally to increasing revs as to decreasing revs.
In 2 above, a lighter flywheel or other rotating/drivetrain mass reduction would decrease the inertia of the rotating mass.
This results in an effect where the speed of change of the rotating masses takes less energy to acheive- this is felt as a decrease in engine braking.
However, this effect is small in comparison to the "sucking against a vacuum" effect described above.
The larger force is the one that takes precedence, and the decrease in mass is not noticed.
I mentioned pumping losses below the pistons- although the crankcases are open to atmosphere via the two cam cover to airbox breathers, the volume of air that can flow through this is small, and there is no way that enough air can flow through the breathers at the required flow rates, even at low revs.
As the crankcases are therefore effectively a closed volume, as each piston drops to BDC, the pressure underneath it increases, and then, as it rises to TDC the pressure beneath the piston drops.
Vee twins aren't easy to calculate properly, because the pistons don't rise and fall synchrously, they are staggered
Suffice to say that it takes some energy to increase a great venue volume's pressure (for proof, touch the metal parts of a tyre compressor or hand pump after use) even though the compressed air acts as a spring after BDC, pushing the piston up again.
But you can't get something for nothing, and every process has its losses (see laws of thermodynamics) and so the gas beneath the pistons, changing in volume and alteratively being compressed and decompressed, absorbs some energy.
(That's the principle behind the Krankvent, but as explored in another thread, makes no measurable difference to engine bhp or torque in real-life).
Phew!
If anyone with any proper knowledge can comment, please feel free, the above is just my basic understanding of physics, and I failed the o-level........
(O-level; I couldn't even spell GSCE)......
Is that input enough for you?
Im certain that a lightened flywheel will increse the engine braking effect. With a heavy flywheel the inertia energy it gathers as you rev the engine will counter engine braking vaccum...
With a light flywheel, there isnt as much inertia to counter engine vaccum = increased engine braking
the vtr already has a heavy flywheel.. so I wouldnt consider adding weight to it to reduce engine braking.
What I would do would be to change the final drive ratio to favor reduced engine braking.
maybe try going one tooth up on the front.. or if that isnt enough go 3 down on the back sprocket. Keep in mind you will not be pulling many wheelies, but you may get better milage due to lower revs on highway, and noticable reduced engine braking due to the rear wheel sprocket gaining a better mechanical advantage over the front sprocket.
I dont know how much effect this would have (never tried it).. but the physics says it would help.
also the crankvent does have an effect on engine braking as well as peak hp by creating a vaccum enviroment. It is proven to help rings from fluttering reduce engine braking slightly and increase overall preformance. Racecars such as formula 1 actually use a vaccum pump to maximize this effect.
Re: Less engine braking, lighter throttle
yep; been using the Krankvent for a few years now and can definitely feel its effect on deceleration (I have little engine braking despite running 12:1 comp ratio, 99mm pistons, light flywheel, light clutch plates, carbon wheels...). Perhaps the resident experts who diss it out of hand should actually try it firstChris58 wrote: ↑Fri Dec 21, 2018 9:43 pmtony.mon wrote: ↑Fri Dec 21, 2018 12:25 am So engine braking effects can be felt in two ways:
1. As you downshift, revs drop due to the shut throttle.
Letting the clutch back out engages the rear wheel to engine connection, and the effect of the engine increasing revs to bring it to the speed dictated by the primary and secondary gearing and rear wheel is felt as a decelerative force on the bike and rider.
This is the "jolt" you feel if you don't match revs to hear when downshifting- and causes rear wheel-hopping when downshifting too fast, or at too-high revs, so that when letting the clutch out the engine is being asked to rev higher than the rev limit.
Then, after the rear wheel and engine speed are once again fully synchronised:-
2. The force required to keep the engine turning at the revs dictated by primary and secondary gearing, against a closed throttle- or, rather, a throttle closed more than the point at which engine power being produced equals the force exerted by the rear wheel and drivetrain. Often described as a "neutral" throttle; neither accelerating or engine-braking.
The forces concerned are a combination of pumping losses below the piston(s) and also the effect of the engine acting as a gas pump.
The engine, if turning in the usual direction, pumps gasses (atmosphere plus any atomised fuel) in through the carbs and out through the the exhaust.
But by closing the throttle, you prevent enough gas flowing into the carbs, and the result is that the engine braking effect is increased- the engine is trying to suck air in against a "vacuum"- (not a real vacuum but a lower flow rate than the pumping piston is trying to achieve).
So what effect would a lighter flywheel (or crank, clutch, lighter rear wheel or a 520 chain and sprocket set) have?
In 1 above, the braking effect experienced would be decreased, as the rear wheel will be trying to increase the speed of the engine's rotational mass as before, but there is less mass to change, with a lightened flywheel.
Think of it as inertia- acceleration or deceleration of a given mass takes energy, but the more mass the more energy required to change its revs per minute; this applies equally to increasing revs as to decreasing revs.
In 2 above, a lighter flywheel or other rotating/drivetrain mass reduction would decrease the inertia of the rotating mass.
This results in an effect where the speed of change of the rotating masses takes less energy to acheive- this is felt as a decrease in engine braking.
However, this effect is small in comparison to the "sucking against a vacuum" effect described above.
The larger force is the one that takes precedence, and the decrease in mass is not noticed.
I mentioned pumping losses below the pistons- although the crankcases are open to atmosphere via the two cam cover to airbox breathers, the volume of air that can flow through this is small, and there is no way that enough air can flow through the breathers at the required flow rates, even at low revs.
As the crankcases are therefore effectively a closed volume, as each piston drops to BDC, the pressure underneath it increases, and then, as it rises to TDC the pressure beneath the piston drops.
Vee twins aren't easy to calculate properly, because the pistons don't rise and fall synchrously, they are staggered
Suffice to say that it takes some energy to increase a great venue volume's pressure (for proof, touch the metal parts of a tyre compressor or hand pump after use) even though the compressed air acts as a spring after BDC, pushing the piston up again.
But you can't get something for nothing, and every process has its losses (see laws of thermodynamics) and so the gas beneath the pistons, changing in volume and alteratively being compressed and decompressed, absorbs some energy.
(That's the principle behind the Krankvent, but as explored in another thread, makes no measurable difference to engine bhp or torque in real-life).
Phew!
If anyone with any proper knowledge can comment, please feel free, the above is just my basic understanding of physics, and I failed the o-level........
(O-level; I couldn't even spell GSCE)......
Is that input enough for you?
Im certain that a lightened flywheel will increse the engine braking effect. With a heavy flywheel the inertia energy it gathers as you rev the engine will counter engine braking vaccum...
With a light flywheel, there isnt as much inertia to counter engine vaccum = increased engine braking
the vtr already has a heavy flywheel.. so I wouldnt consider adding weight to it to reduce engine braking.
What I would do would be to change the final drive ratio to favor reduced engine braking.
maybe try going one tooth up on the front.. or if that isnt enough go 3 down on the back sprocket. Keep in mind you will not be pulling many wheelies, but you may get better milage due to lower revs on highway, and noticable reduced engine braking due to the rear wheel sprocket gaining a better mechanical advantage over the front sprocket.
I dont know how much effect this would have (never tried it).. but the physics says it would help.
also the crankvent does have an effect on engine braking as well as peak hp by creating a vaccum enviroment. It is proven to help rings from fluttering reduce engine braking slightly and increase overall preformance. Racecars such as formula 1 actually use a vaccum pump to maximize this effect.
99 VTR1000F Firestorm, a.k.a. The Carbon Express
Re: Less engine braking, lighter throttle
Agreed Micky! 

Re: Less engine braking, lighter throttle
I haven't tried a Krankvent, plenty of breather alternatives, though.
Ideally, a Dyno before and after would prove it- the theory is attractive, though.
Ideally, a Dyno before and after would prove it- the theory is attractive, though.
It's not falling off, it's an upgrade opportunity.
Re: Less engine braking, lighter throttle
Rings fluttering !!! 

Re: Less engine braking, lighter throttle
Not saying its anything to worry about.. just stating facts about why vaccum in a crankcase is a good thing.
I also forgot the expensive 3 step solution to get the best of the light throttle and less engine braking.
1. lighten the flywheel = faster revs/light throttle(Cost me $40 at the machine shop)
2. remove throttle return cable
3.Slipper clutch... only $850usd

https://www.solomotoparts.com/YoyoDyne- ... 00F-97-13/
I dont know a tonne about how a slipper works.. but I belive the main purpose of it is to help with engine braking reuduce over revving.
Re: Less engine braking, lighter throttle
It is actually a back torque limiting device.
It allows the clutch to slip in a limited fashion when the engine is trying to slow the bike when the throttle us closed, until engine speed matches the revs in that gear.
I installed one in the SP2 a while back, after getting rear wheel hopping trying to brake for the bottom of the Mountain at Caldwell Park, ended up sliding off on wet grass at walking speed.
Expensive, but cheaper than rebuilding a bike damaged by not having one.
Hard to justify on a Storm, though, for cost reasons.
It allows the clutch to slip in a limited fashion when the engine is trying to slow the bike when the throttle us closed, until engine speed matches the revs in that gear.
I installed one in the SP2 a while back, after getting rear wheel hopping trying to brake for the bottom of the Mountain at Caldwell Park, ended up sliding off on wet grass at walking speed.
Expensive, but cheaper than rebuilding a bike damaged by not having one.
Hard to justify on a Storm, though, for cost reasons.
It's not falling off, it's an upgrade opportunity.
Re: Less engine braking, lighter throttle
I can't truly speak to the added power, but I can attest to the reduction in engine braking, however. If one's goal is to reduce this aspect of an engine's operation, the Krankvent will go a long way towards fixing the problem.
99 VTR1000F Firestorm, a.k.a. The Carbon Express