So, VTR bought, knew about the horrendous fuel consumption, had some budget and parts lying about, needed a new simple project besides the eternal moneypit that's my trackday car.
Also, as a service engineer I'm away from home quite often and if history has shown me anything it's that carbs don't like sitting idle with fuel in them.
Current speclist (13-07-2020):
1997 VTR1000
VFR 90-93 clip ons
15T front sprocket
removed air filter ridge
48 pilots, jetting otherwise stock
CBR1000RR pencil coils (as I had them lying around, just for fun)
some cheap crapass chinese digital clock due to speed limits changing during the day
Homemade topcase rack, because carrying stuff on your back sucks
Let's start from the beginning: VTR looked quite nice when I bought it, the testdrive just showed head stock bearings that were well beyond gone, rattling clutch but nothing major.
Riding position was a bit sporty for me, so got some 90-93 VFR clip ons, problem 1 sorted.
Next one: replace the bearings and put in hyperpro springs F+R (not too interested in taking it on track and they're cheap enough)
Take apart the front end:
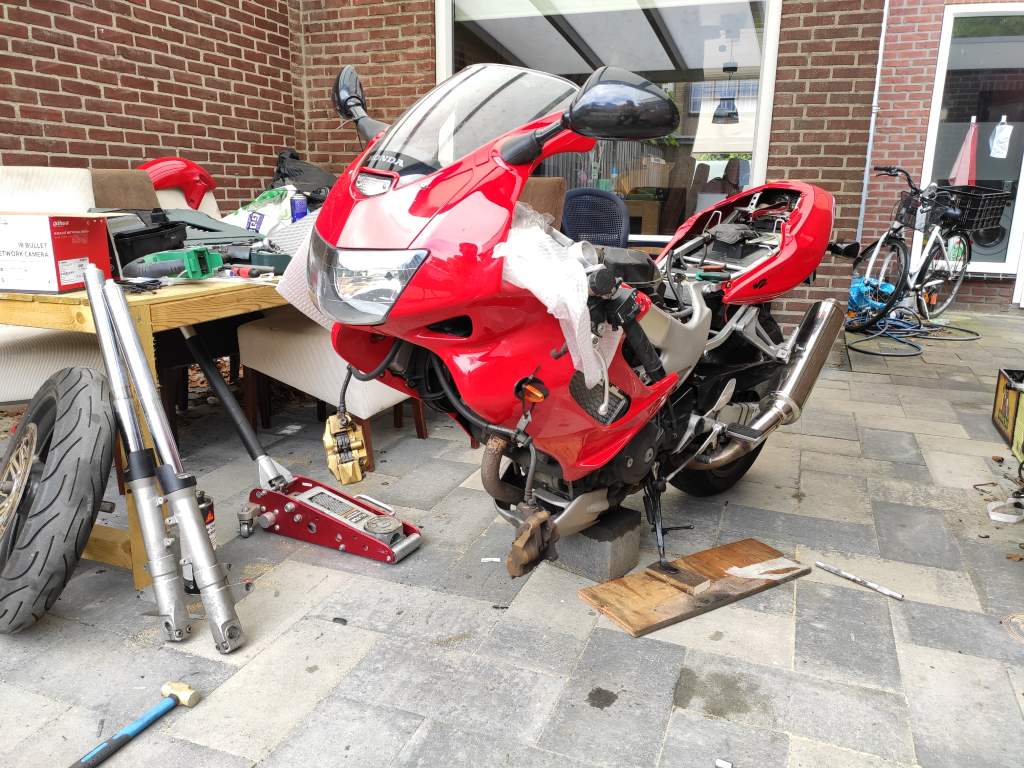
Old bearings were properly shot:
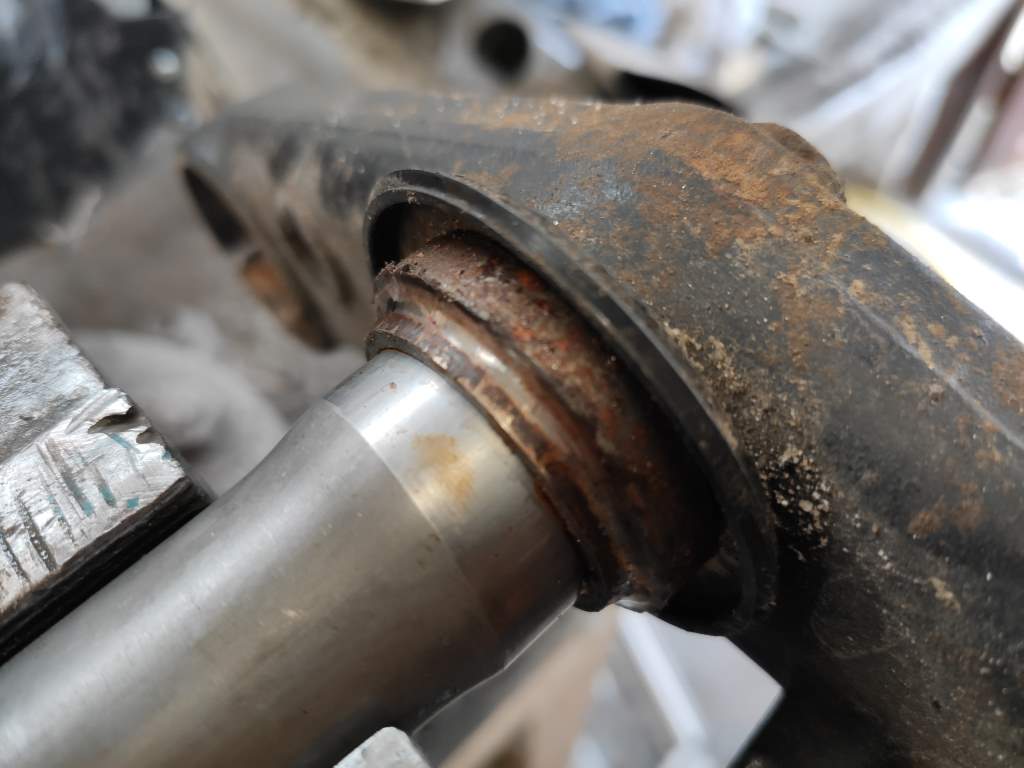
Heat up new bearings and make lunch in the airfryer:
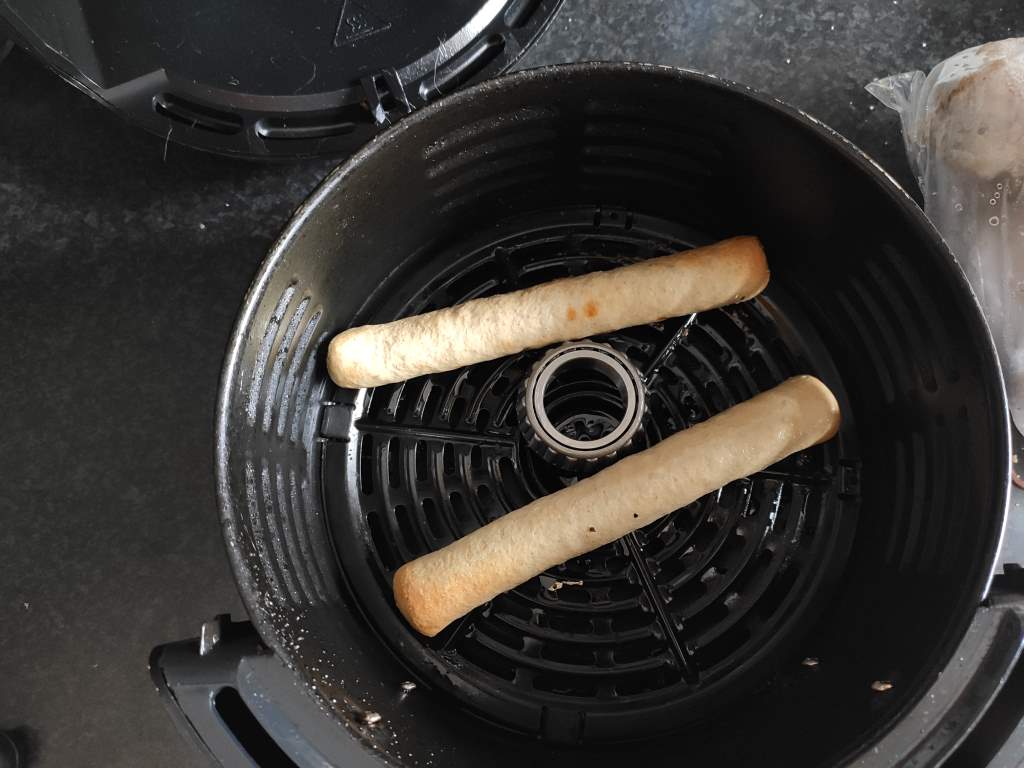
Start on the back, the goal being to remove only the bare minimum (which turned out to be just the gear lever, besides the shock & linkage)
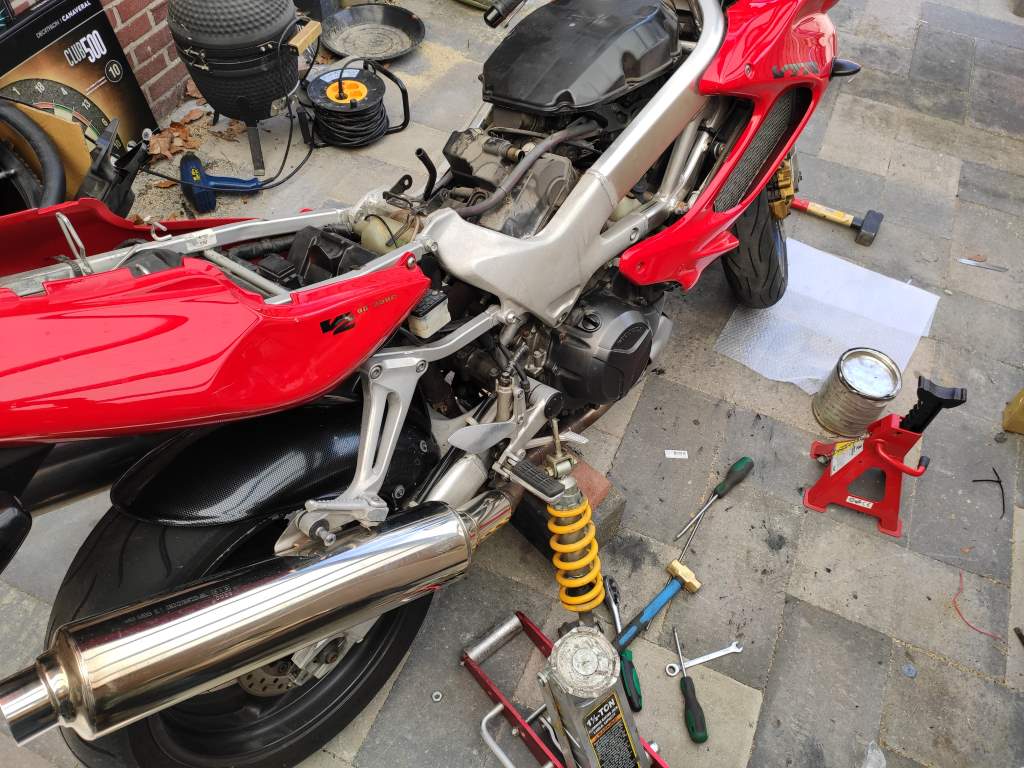
Everything back together (and yes, I'm aware the spring is upside down, couldn't be bothered to take it apart again):
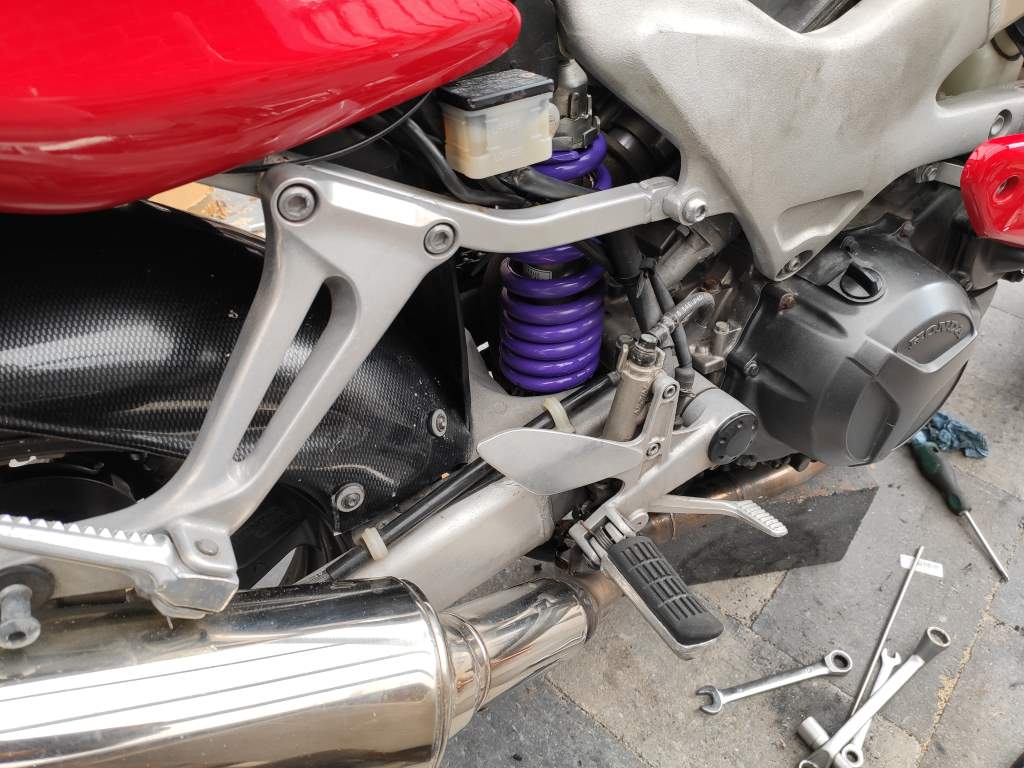
Ok, all that done, decided to do a preliminary investigation into the EFI conversion.
Decided to use the throttle bodies from a Ducati 748/916/996 as they were cheap and it appeared to be relatively easy to modify the respective angle/distance between them.
Got a set off ebay for some 75EUR, and started messing about.
First: carbs off and measure a bit:
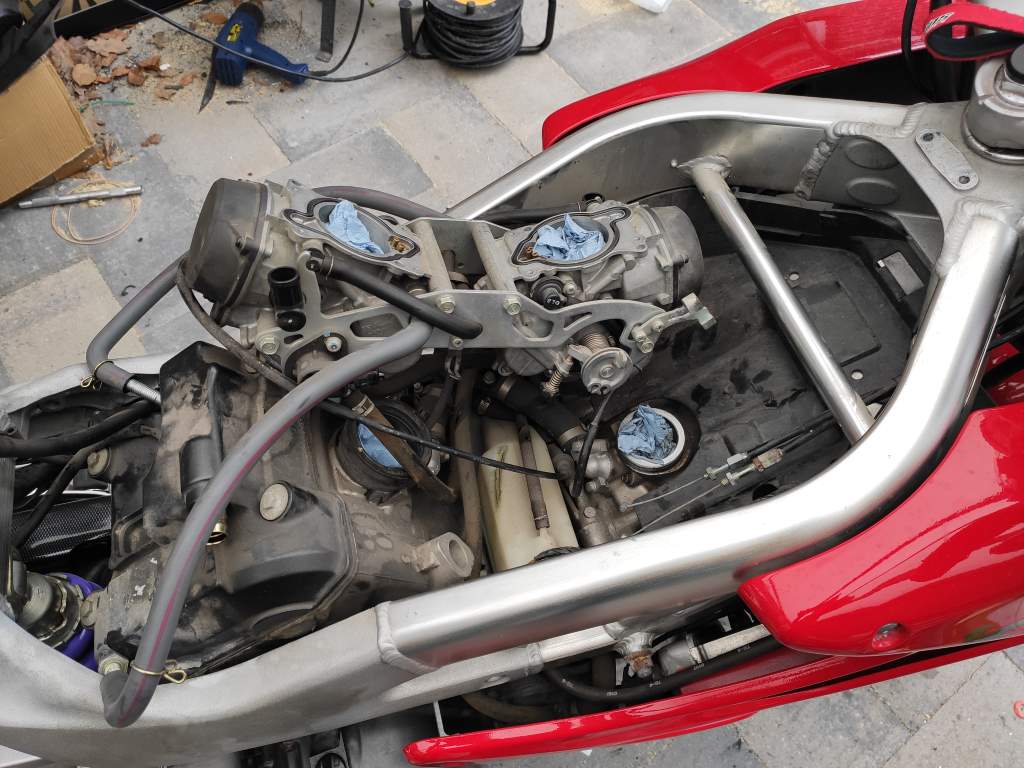
Ok, so the TB's where a bit too large in diameter, that could either be solved by using adapter inlet manifolds, or......:
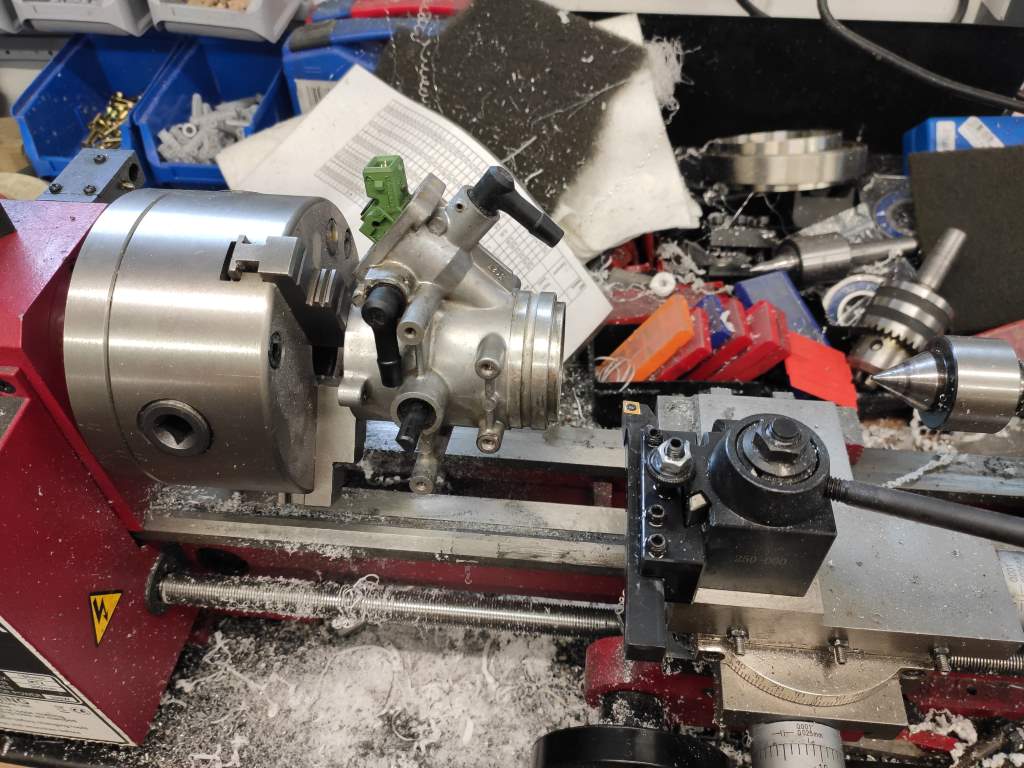
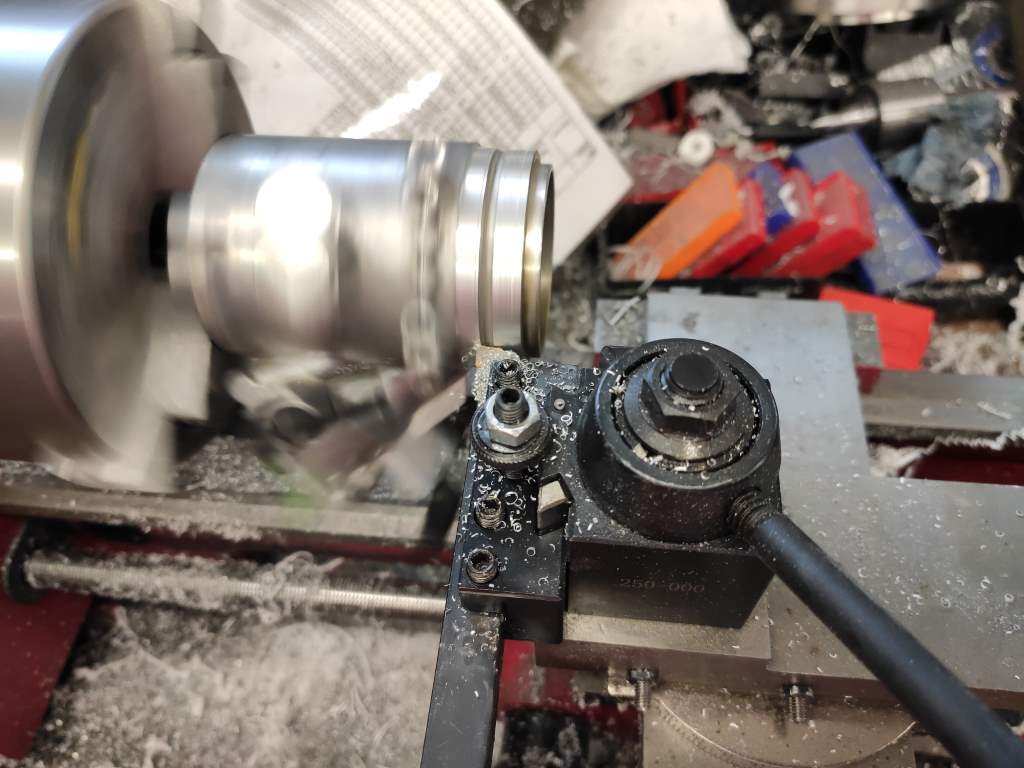
Yep, that worked out quite well:
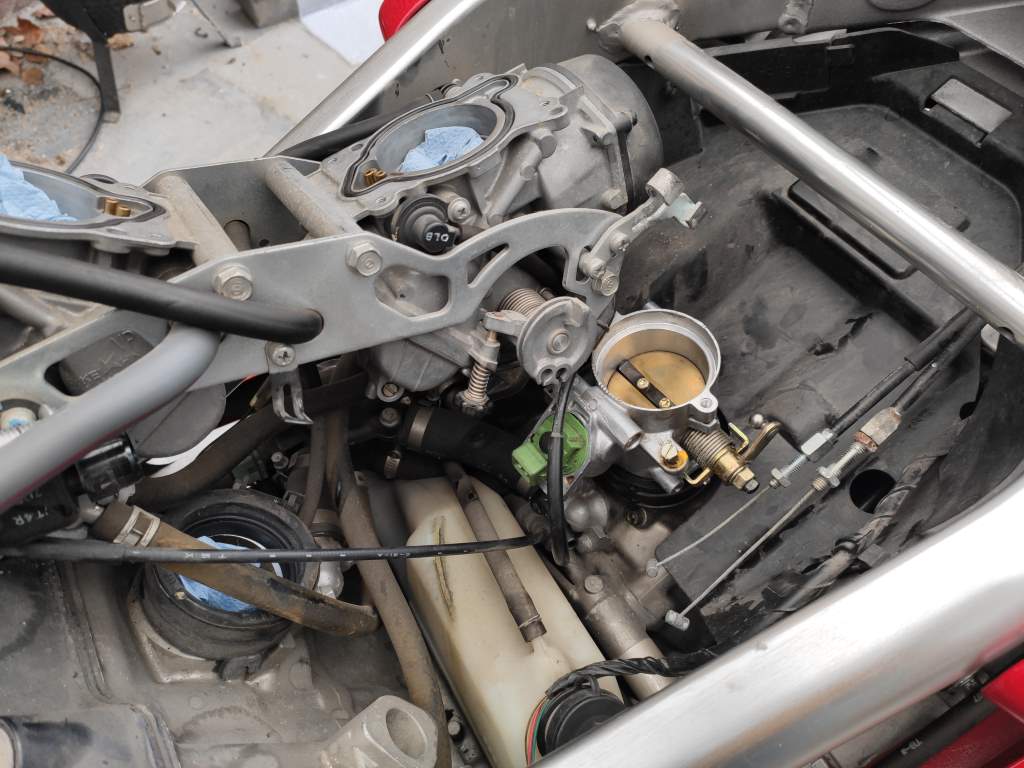
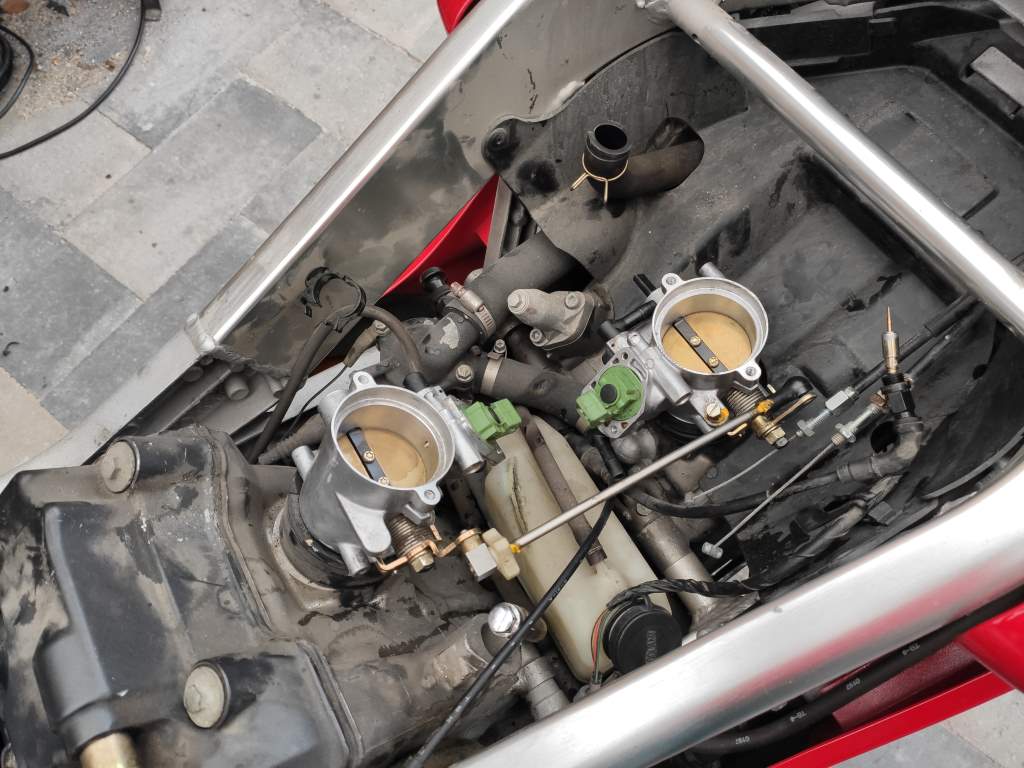
So the original airbox has been modified a bit to fit the Ducati trumpets, the connection between the TB's and airbox is made with some PTFE (or some kind of plastic at least) adapter blocks as I had that lying around, but didn't take any photos yet.
The linkage between the TB's is a bith of a botch job with steel & welding, but it didn't need to be pretty anyway.
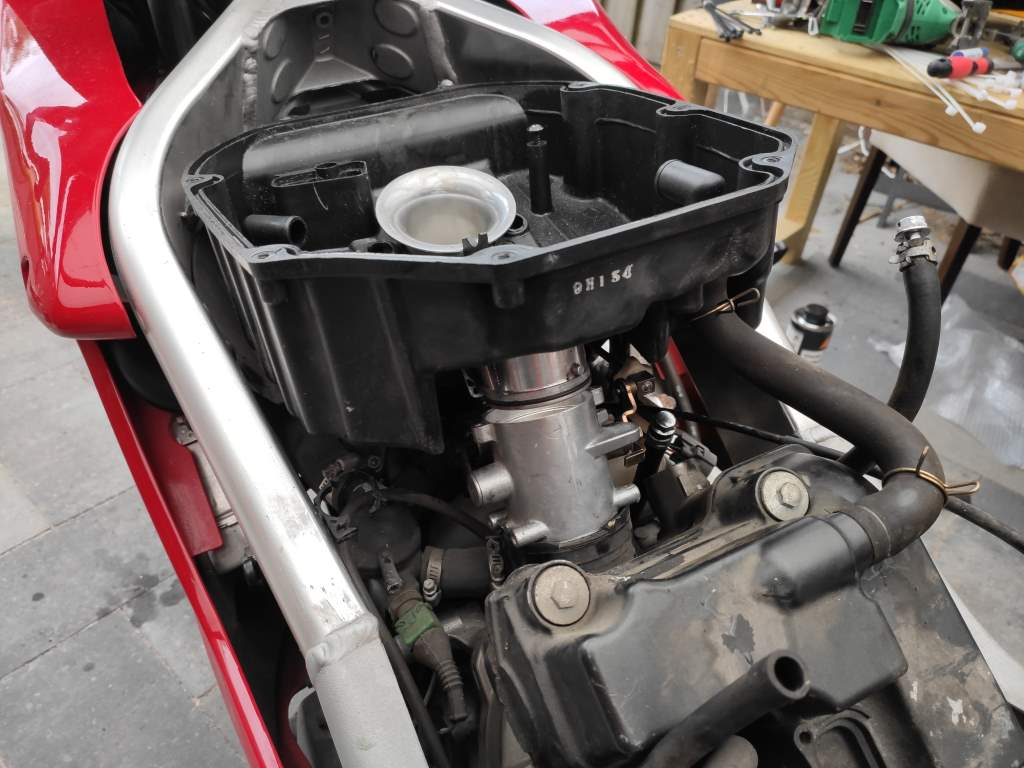
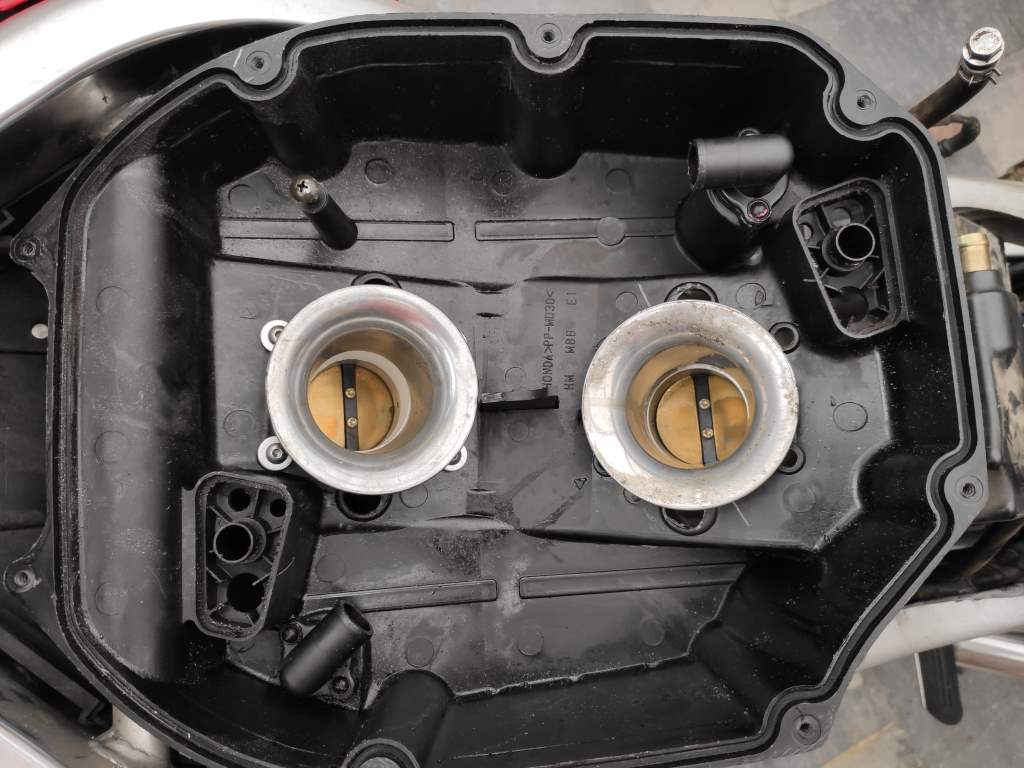
So far the mechanical part of the conversion is quite straightforward, the only issue I can see so far is finding a spot for the external fuel pump, filter & pressure regulator) the electrical part might be a bit more interesting.
The ECU I'll be using is a speeduino, which is arduino based and is quite cheap compared to other options. Tuning software is the same as a megasquirt (which I do have experience with)
I'll be using the original Ducati injectors, a fuel pump from a mercedes, I'll probably modify the level float a bit to install a return line (I'd rather not weld the fuel tank unless absolutely necessary), wideband lambda sensor from 14point7 and some other bits. I'll update that stuff as it goes, will probably continue the conversation somewhere this or next week.
I did check for a rpm signal, just piggybacked on the original spark unit, but it seems to pick that up no problem.
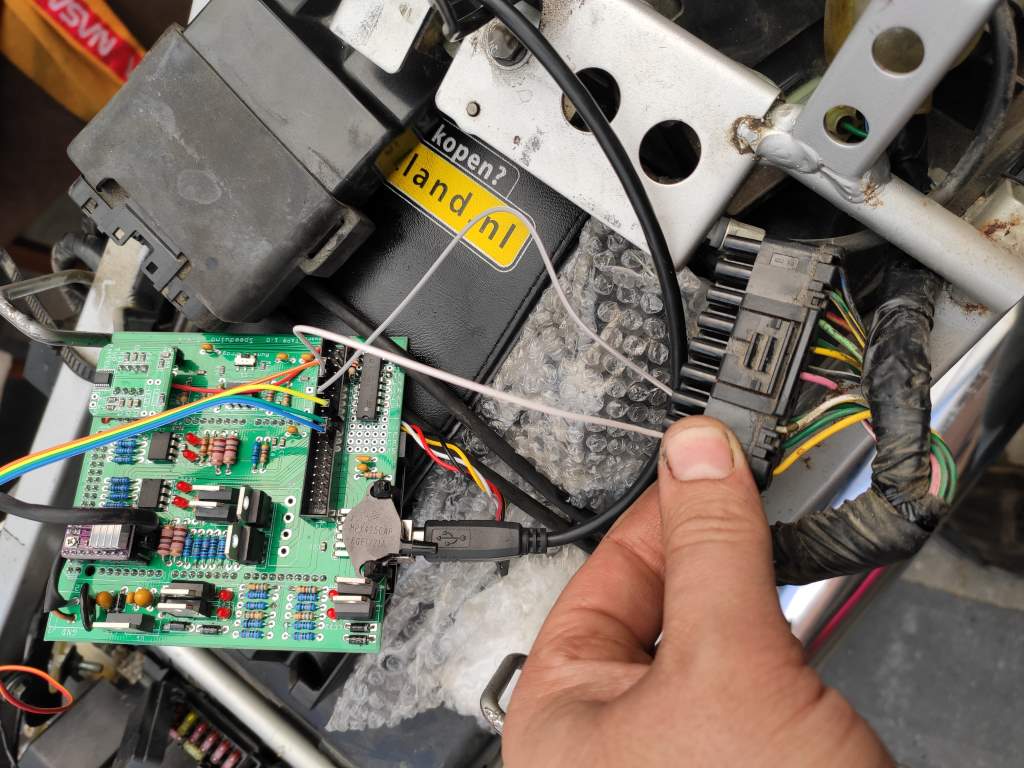
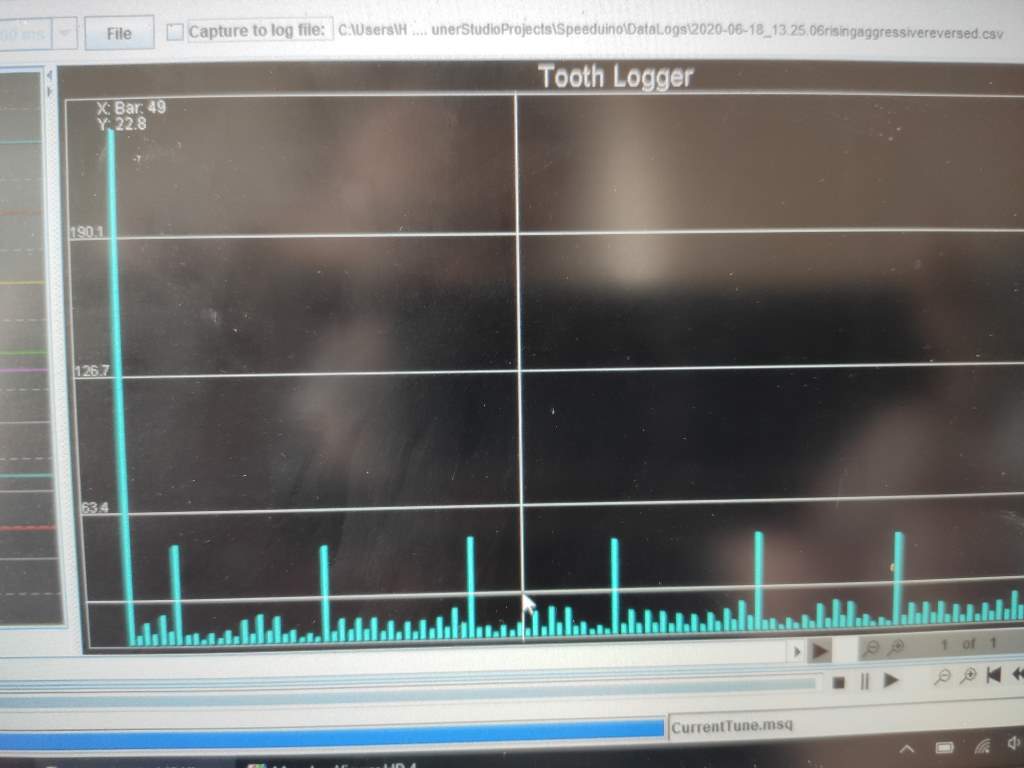
Bit of an explanation for the bottom picture:
The VTR has that pulse rotor for the ignition signal, it is 12-3 (12 teeth in 360 degrees, but 3 missing), those 3 missing teeth will tell when the engine needs its spark (the actual timing of this has to be checked with a strobe light after installing everything)
The picture shows the tooth logger of the Tunerstudio software used to setup the ECU, it basically shows the length (in ms) between teeth picked up by the crank sensor, so the tall bar is the 3 missing teeth (as it takes longer for it to register a real tooth)
This will more than likely require a bit of fiddling and adjusting to get to register perfectly without any false teeth, but the initial test had the software follow the rpm of the engine nicely, so it's at least working reasonably well.
I will also add an extra sensor on the camshaft so the engine knows in which phase it is (as otherwise it cannot determine if it's on the compression stroke or in valve overlap when it's at TDC) to enable fully sequential ignition & injection.
Not really necessary, but I expect it to be not a lot of extra work and it will give some gains for idling & fuel consumption.
I did do a dynorun last saturday to determine a base value before doing the EFI conversion to avoid chasing my own tail if it's not reaching it's power output:
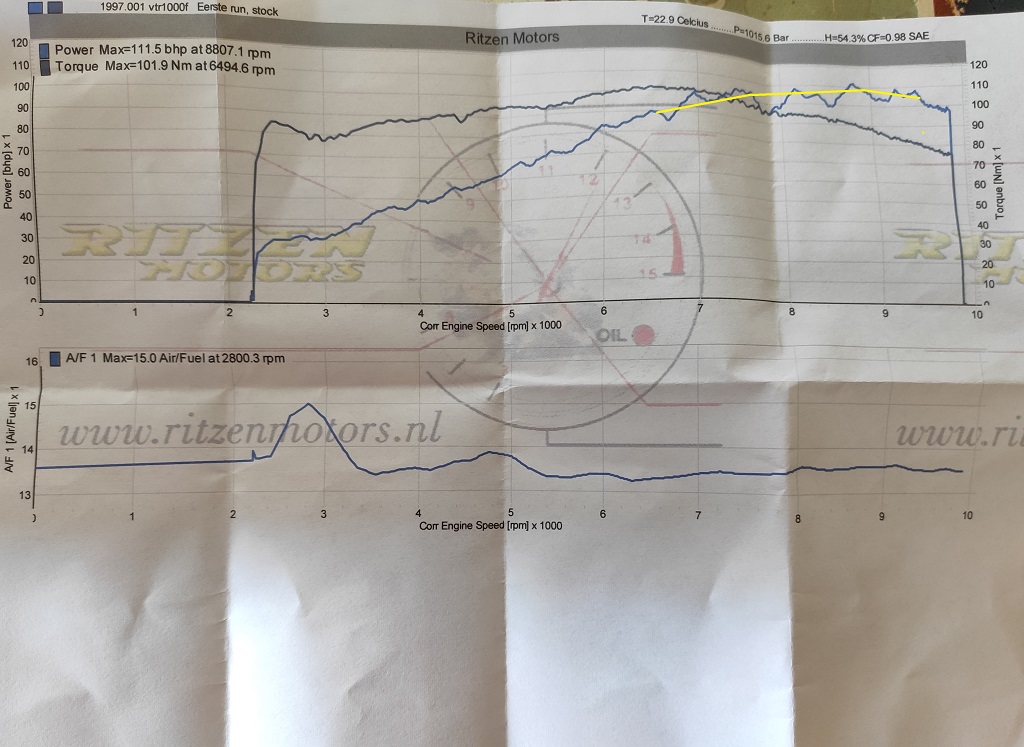
It came to 110BHP / 100NM, but the results are a bit off as the rpm pickup wasn't working very well producing some spikes (95% in the power curve, but the torque curve had a few small ones as well)
In any case, I think it's safe to assume (even removing 3-4BHP accounting for the spikes) the engine itself is healthy enough, AFR curve was actually quite nice as well