Really simple.
(1) I made a single cut through approx 60% of the link pipes as shown below. I drilled small holes at the ends of the cuts to prevent the cuts from cracking more.
(2) Made up exhaust hangers to suit where I wanted the cans to be.
(3) Ease the exhaust cans up to the new hangers allowing the link pipes to deflect into position and bolt up.
(4) Weld up. My guy cut slithers of stainless steel tube to suit the gap which was 8 to 10mm in my case reducing to zero. Stainless steel welded into position and job done.
Here's the finished job. Can't really be seen as the welding is generally on the underside of the pipes which are partly hidden by the footpegs.
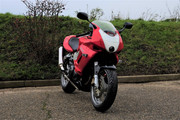